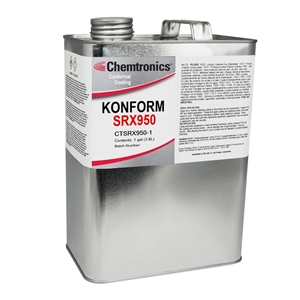
Your Sample Request
Konform SR-X Silicone Conformal Coating
*=required field
TDS
REGS
SDS
Konform SR-X Silicone Conformal Coating
One-part, clear conformal coating with moisture, corrosion and abrasion resistance
Konform SR-X is a one-part, clear conformal coating with moisture, corrosion and abrasion resistance. It was developed to be the best alternative for Dow Corning conformal coating 1-2577 & 1-2620.
Low VOC coating for maximum flexibility and protection from extreme temperatures, harsh environments, and vibration damage
Silicone conformal coatings are the most universal coating, offering protection for a wide variety of environments. This coating offers resilient, mechanical stress-reducing protection. Utilizing a moisture/humidity-based curing mechanism, this coating cures quickly at ambient conditions.
This high-gloss transparent conformal coating provides ideal protection for both rigid and flexible printed circuit boards. Cured coatings are hydrolytically stable and retain their physical electrical properties after high temperature and humidity exposure.
Konform SR-X is high viscosity, 950 CPS (+/-100), so can be used for the thickest final coat in a dipping application, or thinned for spray systems.
Features & Benefits
- Engineered for applications where flexibility and high temperature resistance are required
- Exceptional dirt, dust, and soil repellency -- surfaces remain clean longer
- Superior transparency
- Superior corrosion resistance
- Low VOC
- Low toxicity – HAPs free
- Silicone coating stable from -76°F/-60°C to 392°F/200°C
- High dielectric strength of 720 volts/mil
- Easily removed with Electro-Wash® Two Step or CircuitWorks® Conformal Coating Remover Pen
- Contains a UV indicator for quality control inspection
- RoHS Compliant
TDS | |
REGS | |
SDS | |
Categories |
Specifications |
|
---|---|
Shelf Life | 1 yr |